[ad_1]
Welcome to Thomas Insights — every day, we publish the latest news and analysis to keep our readers up to date on what’s happening in industry. Sign up here to get the day’s top stories delivered straight to your inbox.
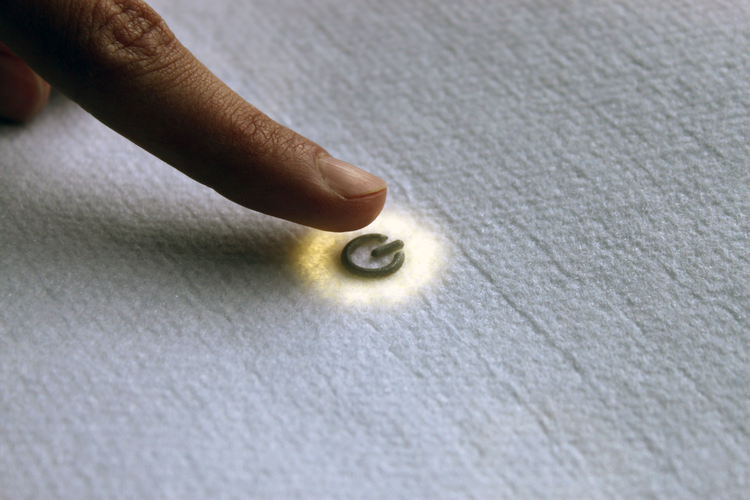
This article is sponsored by LOOMIA Technologies, Inc., a custom manufacturer of soft, flexible circuits that provide electromechanical solutions for next-generation products.
Engineers and industrial designers often use electronic textiles to give their products extra functionality including pressure sensing, lightweight cabling, and heating.
“When people think of electronic textiles, they’re often thinking of a conductive thread in a fabric,” says Madison Maxey, founder and CEO at LOOMIA Technologies, Inc. “But there are a wide range of different kinds of e-textiles; just like there are technical textiles that go into making tires, there are e-textiles that go into these very industrial projects and can be laminated or added on with a pressure-sensitive adhesive. E-textiles don’t always have to follow traditions of garment making or fabric techniques.”
With the launch of LOOMIA in 2005, Maxey officially debuted the LOOMIA Electronic Layer (LEL), an innovative, patented electronic textile that can be attached to an A-surface material of choice through sewing, heat bonding, or pressure-based adhesives and is unlike other e-textiles on the market.
Thomas Insights (TI): What sets LOOMIA apart from your competitors in the electronic textile space?
Madison Maxey (MM): We’re a little different from other kinds of circuit or even e-textile technologies because we build our circuits for easy integration. They’re also very scalable and robust. We use reliable materials for constructing products that need some sort of electronics in them. Often when people hear e-textiles, they think of something sewn by hand or something that’s fragile. But we knew the technology had to be scalable for mass-manufacturing in an electronics factory, and we wanted it to be robust and reliable so that it wouldn’t be a delicate thing that couldn’t go into consumer products. At LOOMIA, we use a laminated technique, and we test our products for automotive environmental cycling, for example.
We’re also different from traditional circuits or even flex printed circuit boards (PCBs). Our cutting-edge LEL adds a level of comfort that PCBs and wires cannot provide, featuring a low resistance of 0.03 Ω per square and multi-functionality in a single circuit to streamline assembly. Our technology has multi-axis flex, and it tends to flex over and over again. Unlike a flex PCB, you can bend our materials multiple times and they’ll continue to function well. They’re ideal for tough electromechanical problems.
TI: Are LOOMIA products best suited to particular applications?
MM: The application is always something that has some level of misconception around it. When people hear “soft, flexible circuits,” they typically associate that with fashion applications. However, we found that most of the applications for which engineers have electromechanical problems tend to be the more industrial ones, which technology like ours can solve.
Beyond wearable technology, our products’ strongest applications are actually in things like soft robotics, automotive interiors, outdoor gear, healthcare and wellness products, or even consumer products that have a soft-goods element. People are always really surprised when they hear that we use e-textiles for these use cases.
The products we make are a little bit between design and engineering. We may have an industrial designer saying, “I want to use this for the product, but I’m going to need a lot of information about how the electronics work.” Sometimes it’s an electrical engineer, who says, “I know how to do all of this, but it needs to be tweaked to really fit my product.” So it depends on who the customer is.
Generally, there’s a high level of customization involved because we offer a limited number of standard parts, and the base technology is customizable and allows for different kinds of circuit designs. We work collaboratively with our customers’ teams to get our circuits integrated where they need them. Also, we’re constantly sourcing lower-cost materials so that we can be more competitive and actually get things on the market rather than just having a specialty product.
One of our most exciting recent partnerships was with Covestro, a high-tech polymer material supplier. We collaborated with them to develop a roll-up sunroof shade demonstrator that both heats and lights in order to provide heating for the interior of an electric vehicle, which cannot draw heat from an internal combustion engine.
We also recently worked with Festo, an automation technology company, to create an analog pressure matrix that was fully integrated into a glove for their BionicMobileAssistant. The 100+ point analog pressure matrix gave the robotic mobile system a sense of touch through its pneumatic-controlled gripping hand. Whenever we’re working on client projects, we’re always pushing the limits!
TI: At what stage in the product development process do customers usually approach the LOOMIA team?
MM: Mostly, we have clients come to us and say, “We tried the normal stuff. It’s not working for our application.” That’s when it’s really exciting.
Oftentimes, customers will come to us with some sort of initial validation done where they might have built a prototype or tried out the concept earlier, but they want to make it something that’s closer to production. That’s when we tend to get involved.
When working with LOOMIA, customers can request free sample components like heaters and pressure matrices, and our lab will generate a works-like, looks-like prototype ideal for testing. LOOMIA also has prototyping parts available online through Digi-Key Electronics, SparkFun Electronics, and Adafruit. We have buses, pressure sensors, user interfaces with a collection of functionalities, and heaters.
I really enjoy when customers show us something they’ve done with our prototyping parts, like when someone tells me, “We used your parts to build this first version, and now we want to make it better and more custom.” Then we work from there. We try to make it as easy as possible to test drive the technology. We have prototype parts, but we also have marketing demonstrators. You can plug them in and test things like heaters and switches.
TI: Are you noticing any industry trends that will likely be pertinent to your product?
MM: Definitely. It seems like there’s a new wave of wearables coming where they’re more thought-out and functional. When I started working in this space in 2012, everyone had all these ideas, but they were never going to be feasible for a product. But I think we’re seeing a lot more products that people might truly love.
There’s a huge industry trend involving automotive interiors as well. With electrification happening, I anticipate a number of future design changes. Some companies are changing interior fabrics, trying to make things look sleeker and more streamlined by removing plastic buns and housings. So I think there’s a big movement toward using e-textiles or smart fabrics in automotive interiors, which I’m very excited about.
Image Credit: Image courtesy of LOOMIA
More from Engineering & Design
[ad_2]
Source link